Rockwell saiakuntza metalezko materialen gogortasuna neurtzeko erabiltzen den saiakuntza bat da, ISO6508-2 arauari jarraituz gauzatu beharrekoa. Gogortasuna materialek duten berezko propietatea da.
Material baten gogortasuna honela definitu ohi da: materialak deformatzeko erakusten duen erresistentzia, beste gorputz bat bere gainazalaren kontra bultzatzean. Beste modu batean esanda, bere kontra eginiko indarraren eraginez markarik ez agertzeko materialak erakusten duen erresistentzia da gogortasuna.
XX. mende hasieran, ikerlariak konturatu ziren lotura estua zegoela gogortasunaren eta pieza edo makina desberdinetan agertzen ziren akats mekanikoen (adibidez, gainazal-akatsak) artean. Hortaz, gogortasunaren ezaugarriak aztertzen hasi ziren.
Aztertzen hasi bezain laster, material desberdinen gogortasuna neurtzeko saiakuntza bide desberdinak asmatu ziren. Lehenengoa Brinell saiakuntza izan zen, 1904an, hain zuzen. Dena den, aztarna handiak uzten zituen, eta oso motela zen. Gainera, ez zen eraginkorra gogortze-tratamenduak zituzten burdinen kasuan (tresna-altzairuak, altzairu aleatuak, aleazio desberdinak, …).
Ondorioz, 1914an, Hugh M. Rockwellek eta Stanley P. Rockwellek Rockwell saiakuntza-makina asmatu zuten. Horri esker, guztiz aldatu ziren gogortasun-neurgailuak. Izan ere, makina honek saiakuntza desberdinak egitea ahalbidetzen zuen (zapaltzaile motaren arabera). Horrela lortutako emaitzak adierazteko eskala desberdinak sortu zituzten; eta horri esker, balio askoz ere zehatzagoak lortu zituzten.
Hainbat eskala daude Rockwell saiakuntzan lortutako emaitzak adierazteko. Eskala bakoitzak emaitzak adierazteko modu desberdin bat dauka.
- Diamantezko konoa (A, C eta D eskalak): HR sinboloaz adierazten da, eskalaren letra adierazgarria amaieran gehituz. Adibidez: 59 HRC (59-ko Rockwell gogortasuna C eskalan neurtua)
- Burdin edo karburozko esfera (B, E, F, G, H eta K eskalak): HR sinboloaz adierazten dira. Amaieran, eskalaren letra adierazgarria eta erabilitako zapalgailua adierazten duen letra bat gehitzen zaio (W karburozkoentzat eta S burdinazkoentzat). Adibidez: 60 HRBW (60-ko Rockwell gogortasuna B eskalan adierazia eta karburozko esfera batekin burutua).
Saiakuntza hau azkarra eta erraza da egiteko, baina ez da aurreko bi metodoak bezain zehatza. Material bigun zein gogorren (altzairu tenplatuak ere bai) gogortasunak jakiteko balio du, baina metodo honetan, azalera kontuan hartu beharrean, sakonera neurtuko dugu.
Sargailu mota bi daude materialen gogortasunaren arabera: material gogorrentzat forma konikoa (erpinean 120º-ko angelua) duen diamantea, eta material bigunentzat, berriz, altzai- ruzko esfera. Beraz, bi gogortasun zehaztu daitezke Rockwell metodoan: HRB –material bigunetan– eta HRC –material gogorretan.
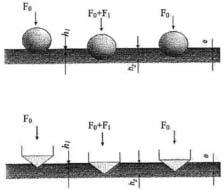
- Material gainean sargailua dago (edo bola, edo konoa), eta karga txiki bat ezartzen zaio (F0, edo 3 edo 10 kg); ondorioz, sakonera txikiko (h1) marka eragin da materialean. Puntu horretan, makinaren neurgailua zeroan jarri da.
- Kargak handitu egiten dira: 90 kg gehiago bola-sargailuarentzat eta 140 kg kono-sarga- iluarentzat. Karga berria hiru eta sei segundo bitartean mantendu ondoren, eragindako sakonera (h2) neurtu egiten da.
- Karga gehigarriak kentzerakoan, sargailua gorantz doa materialaren elastikotasunagatik, baina deformazio plastikoen ondorioz, azken sakonera hasierakoa baino handiagoa izago da (h1+e). Makinaren neurgailua zeroan jarri dugu hasierako karga ezartzerakoan; horregatik, orain, sakonera (e) zuzen-zuzen neurtzen du.
Rockwell gogortasuna honela kalkulatuko dugu:
Material bigunak: HRB=130-e
Material gogorrak: HRC=100-e
Ondoren, Rockwell gogortasunaren adibide bat adierazten da:
600 HV 90/5
Adierazpen horretan, materialaren gogortasuna 600 da, ezarritako karga 100 kg-koa da, eta karga gehigarriak 5 segundo iraun du.
Metodo honen abantailarik handienak hauek dira:
- Azkar egiten da, eta zehaztasunez (edonork egin dezake).
- Markak txikiagoak dira Brinell metodoan baino.
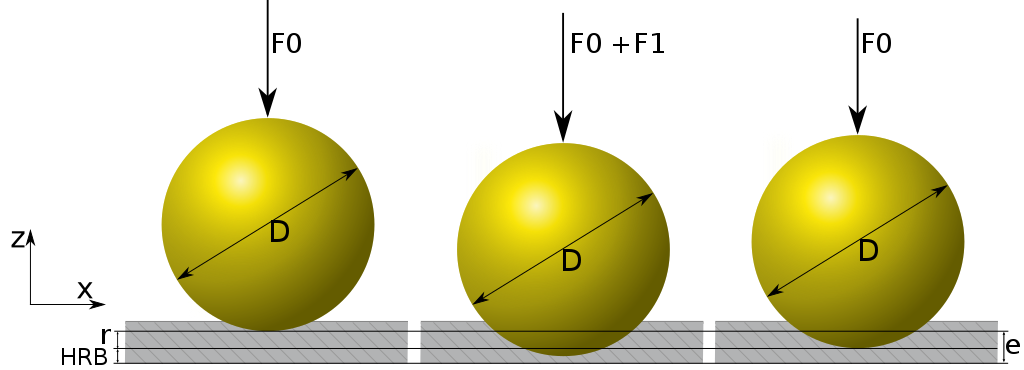
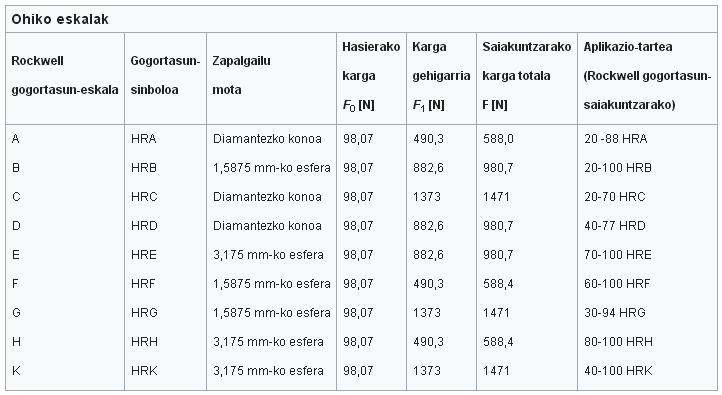
Rockwell gogortasuna hurrengo formularen bitartez kalkulatzen da, h, N eta S direlakoen balioak erabiliz.
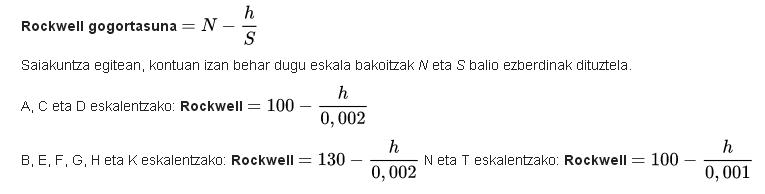
Ariketa nola egin:
Saiakuntza erraza da eta sekuentzia honi jarraitzen dio:
Lehenik, 10 kp-ko aurrekarga aplikatzen zaio sargailuari. Aplikazio horren ondorioz, h0 sakonerako materialean arrasto bat dagoela ikusten da.
Jarraian, karga gehigarri bat aplikatzen da (140 kp Rockwell C-rako eta 90 Rockwell B-rako) segundo batzuetan. Horrela, sortutako aztarnak h1 sakonera handiagoa lortzen du.
Azkenik, karga gehigarria kenduko dugu. Sarkailuak atzera egiten du materialaren berreskuratze elastikoaren ondorioz, h sakonera iraunkorra geratuz. Sarketa, deformazio iraunkorrari dagokiona, e, eta aurreko irudiaren zerrenda laranjan irudikatuta ikusten duguna, sakonera iraunkorrari h, hasierako sakoneraren balioa, h0 kenduz lortzen da. Sartze hori eskala graduatu batean neurtzen da, sargailuak eragiten duen gailu baten bidez.
Eskala 1 mm-ko 100 zatitan dago, zati bakoitza 10 mikraren baliokidea delarik. Erlojuaren indikazioen eta puntaren mugimenduaren arteko erlazioa 5 eta 1 artekoa dela jakinda, eskalaren banaketa bakoitza 2 mikra direla ondorioztatzen da. Horrela, bada, Rockwell unitate bat 2 mikraren baliokidea da, eta zabaleraren guztizkoa 200 da.
Agerian utzi dugunez, Rockwell C-ren (HRc) eta Rockwell B-ren (HRB) arteko aldea erabilitako sarkailuak zehazten du. C aldaerak diamantezko kono bat erabiltzen duen bitartean, B aldaerak esfera bat erabiltzen du. Horrek ere ondorioak ditu gogortasuna kalkulatzeko moduan. HRCn, gogortasuna kalkulatzeko, 100 balioari deformazio iraunkorraren balioa kentzen zaio. HRBn, kendu zaion balioa 130era igotzen da (Ikusi formulak saiakuntzaren irudian).
Bi kasuetan neurgailuak zuzenean erakusten ditu aldeak, eskala desberdinetan, karga gehigarria kentzean. Diferentziak gogortasunaren neurritzat hartzearen arrazoia, sartzearen ordez, gogortasunik handiena (e balio txikiena duena) irakurketa handienari ere dagokiolako da. Horrela, material bigunek material gogorrek baino gogortasun-neurri handiagoak lortzea saihesten da.
Bibliografia: Wikipedia, Elhuyar eta La Tenacilla Tenaz bloga